Тема: Ремонт ковшів та механізмів підйому екскаваторів. Ремонт засобів сигналізації. 03.04.24
Екскаватори – це землерийні машини для розробки ґрунту і перемі- щення його у відвал або до транспортних засобів. За характером роботи роз- різняють екскаватори циклічної (одноковшові) і безперервної дії (багатоков- шові) Всі операції (копання, транспортування ґрунту, розвантаження, повер- нення ковша до забою) екскаватори одноковшові виконують послідовно, а багатоковшові – одночасно, коли один чи кілька ковшів копають, другі – транспортують, треті – розвантажують, четверті – рухаються в забій.
Екскаватори циклічної дії універсальні, вони обладнані більшою кількіс- тю змінних робочих органів з великими технологічними можливостями, ши- роким діапазоном різних видів виконуваних робіт. Екскаватори безперервної дії призначені для виконання значних обсягів однотипних робіт. Вони проду- ктивніші й менш металомісткі.
Екскаватори циклічної дії (одноковшові) за призначенням поділяються на будівельні – для земляних робіт, навантаження і розвантаження сипких матеріалів; будівельно-кар'єрні – поєднують функції будівельних і кар'єрних екскаваторів; кар'єрні – для добування будівельних матеріалів та корисних копалин відкритим способом; розкривні – для зняття верхнього шару ґрунту чи гірської породи перед кар'єрними розробками; тунельні і шахтні – для ро- боти під землею при будівництві підземних споруд та добування корисних копалин. Одноковшові екскаватори з одним чи кількома видами робочого обладнання називають спеціальними або універсальними. Розкривні й кар'єрні екскаватори мають однакову базову машину й відрізняються розмірами робочого обладнання. Розкривні розробляють менш тверді ґрунти, тому для підвищення продуктивності їх оснащують ковшами більшої місткості і вони мають більші габаритні розміри. Шахтні й тунельні екскаватори характери- зуються меншими габаритними розмірами ковшів, тому їх використовують в тісних умовах.
До будівельних належать екскаватори з ковшами місткістю від 0,15 до 4 м3, які розробляють ґрунти І – IV категорій. Такі екскаватори – універсальні
машини і мають різні види змінного робочого обладнання – землерийного та іншого призначення: для навантажувально-розвантажувальних робіт; монтажних; пальових; планувальних тощо).
Марки екскаватора позначаються літерами ЕО, чотирма цифрами і двома буквами (останніх може не бути). Букви ЕО характеризують екскаватор як одноковшевий універсальний. Чотири основні цифри означають: розмірну групу машини, тип ходового обладнання, конструктивне виконання робочого обладнання та порядковий номер моделі. Вісім розмірних груп екскаваторів позначаються цифрами від 1 до 8. Цифра 1 відповідає місткості основного ковша 0,15 м3; 2 – 0,25 м3; 3 – 0,4 м3; 4 – 0,65 м3; 5 – 0,25 м3; 6 –1,6 м3; 7 – 2,5
м3; 8 – 4,0 м3. Розмір екскаватора характеризують маса машини, потужність основного двигуна і геометрична місткість основного ковша. Основним ро- бочим органом є ковш, яким екскаватор може розробляти ґрунт I – IV кате- горії. Основні робочі параметри при виборі екскаваторів є глибина та радіус копання, радіус і висота розвантаження тощо.
У стандартах на екскаватори для кожної розмірної групи часто наводять кілька розмірів ковша – основного і змінних підвищеної місткості, при цьому для останніх передбачено значно слабші ґрунти, ніж при роботі з основним ковшем. Тип ходового обладнання екскаваторів вказують цифрами від 1 до 9. Цифра 1 означає гусеничне ходове обладнання; 2 – гусеничне розширене; 3 – пневмоколісне; 4 – спеціальне шасі вантажного автомобіля; 6 – шасі се- рійного трактора; 7 – причіпне ходове обладнання; 8 – плавуче обладнання; 9 – резерв. Конструктивне виготовлення робочого обладнання позначене цифрами 1 (з гнучкою підвіскою); 2 (із жорсткою); 3 (телескопічне). Остання цифра індексу означає порядковий номер моделі екскаватора. Перша з додаткових букв після цифрового індексу (А, Б, В і т.д.) – порядкова модернізація даної машини, наступні – вид спеціального кліматичного виготовлення (ХЛ – для півночі; Т – для тропіків; ТВ – для робіт у вологих тропіках). Наприклад, індекс ЕО-3322 А розшифровується так: екскаватор одноковшовий універсальний, третьої розмірної групи, на пневмоколісному ходовому обладнанні, з жорсткою підвіскою робочого обладнання, друга модель, пройшла першу модернізацію. Екскаватор обладнують основним ковшем місткістю 0,4 м3, який відповідає третій розмірній групі, та змінним – місткістю 0,65 м3.
Екскаватори конструктивно виконані з гнучкою (канатно-блокова система керування робочим обладнанням) і жорсткою (гідравлічна система) підвіскою робочого обладнання мають відповідно механічний та гідравлічний приводи всіх механізмів. Жорстка підвіска дозволяє повніше використовувати масу екскаваторів для реалізації усіх зусиль на зубцях ковша, забезпечує вищу продуктивність.
Екскаватори з телескопічним робочим обладнанням виготовляють з гідравлічним приводом. Вони універсальні, але малопродуктивні й мають ви-
соку вартість. Частіше їх виготовляють повноповоротними – кут повороту поворотної частини в плані не обмежений.
Екскаватори з механічним приводом, конструктивні схеми, призначення
Екскаватори з механічним приводом переважно виготовляють за одно- моторною схемою.
Конструктивна схема одноковшового екскаватора наведена на
Ходовий пристрій 1 – гусеничний забезпечує реверсивне пересування екскаватора.
На рамі ходового розміщено опорно-поворотний пристрій 2 і механізм повороту. На першому змонтована поворотна платформа 14.
На поворотній платформі закріплено двигун внутрішнього згоряння (ДВЗ) 4, противага 3, багатобарабанна лебідка, механізми привода і керування. Зверху все це закрито кузовом, у передній частині поворотної платформи встановлено робоче обладнання. Основними його видами у механічних (канатно-блокових) екскаваторів є: "пряма", "зворотна" лопати; драглайн; грейфер; кранове обладнання.
Крім того, екскаватор можна оснащувати обладнанням для планування на- сипів і майданчиків, розпушування мерзлих і скельних ґрунтів, занурення паль.
Робоче обладнання – "пряма лопата" має стрілу 12 (рис. 1, б), шарнір- но закріплену на поворотній платформі. В екскаваторів 2-ї і 3-ї розмірних груп рукоятка 17 прикріплена до стріли шарнірно. У більших типорозмірів вона частіше з'єднана зі стрілою через сідельний підшипник, який дає змогу повертати рукоятку відносно стріли й переміщувати вздовж осі (напір). Для цього випадку є спеціальний напірний механізм 13.
До рукоятки нерухомо приєднаний ковш 9 із днищем 10, що відкривається. Кут нахилу стріли можна змінити за допомогою стрілового поліспаста 5, канат якого намотується на стріловий барабан 6. Піднімання і опускання ковша здійснюється за допомогою підіймального поліспаста 7,
канат з якого намотується на барабан 15.
Напірні механізми виготовляють з канатним або зубчасто-рейковим
приводом переміщення. Схему напірного механізму з канатним приводом та однобалковою рукояткою наведено на рис. 1, б, стріла двобалкова. Канат, що звисає з підіймального барабана 15, охоплює блок 6, встановлений на верхній частині стріли, зрівноважувальний блок 8, який розташований на ко- вші 9, та блок б. Другий кінець цього каната закріплено на барабані 17 напір- ної лебідки. Барабан встановлено на осі стріли й приводиться в рух ланцюго- вою передачею 18. На барабані 17 закріплено кінці каната 19, який охоплює обидва блоки 20, розташовані на осі сідельного підшипника, та зрівноважу- вальний блок 21 на рукоятці.
При обертанні барабана 17 за стрілкою годинника канатом 19 і проти неї – канатом 22 рукоятка відповідно висувається і прибирається, відбувається незалежне від роботи механізму піднімання ковша.
– Одноковшовий екскаватор з робочим обладнанням "пряма лопата":
a – конструктивна схема; б. в – схеми напірних механізмів; г – схема відкривання днища ковша; 1 – ходовий пристрій, 2 – опорно-поворотний пристрій; 3 – противага; 4 – двигун внутрішнього згоряння; 5, 7 – стріловий та підіймальний поліс- пасти; 6 – обвідні блоки стріли; 8, 21 – зрівноважувальний блок відповідно підіймального механізму і рукоятки; 9 – ковш; 10 – днище ковша; 11 – рукоятка; 12 – стріла; 13 – напірний механізм; 14 – поворотна платформа; 15, 16 – підіймальний і стріловий барабани; 17 – барабан напірної лебідки; 18, 24 – ланцюгові передачі; 19, 22 – канати відповідно висування і повернення рукоятки; 20 – обвідні блоки напірного механізму; 23, 25 – вали; 26 – шестерня; 27 – балка рукоятки;28, 31 – блоки; 29 – важіль; 30 – пневмоциліндр; 32 – допоміжний канат відкри вання днища ковша; 33 – засувка
При вимкненій ланцюговій передачі й обертанні барабана 15 піднімається ковш. За рахунок зусиль, які виникають при копанні, другий кінець підіймального каната повертає барабан 17 і забезпечує автоматичне висування рукоятки. При цьому досягається плавна робота підіймального та напірного механізмів й легкість керування переміщеннями ковша.
Практика показала, що напірне переміщення, що створюється, не забезпечує копання ґрунту при оптимальному куту різання тому використовується комбінований напір, який реалізується при обертанні барабана 17 і періодичному вмиканні барабана 15. Копання, що виконувалося в основному за схемою залежного напору, відбувається з меншими
збитковими зусиллями і за- тратами потужності, холості рухи здійснюються за допомогою незалежного напору, що забезпечує їх швидкість та чіткість.
Екскаватор із обладнанням "пряма лопата" призначений для розробки ґрунту вище рівня стоянки. Часто, щоб підготувати забій, такий екскаватор може копати ґрунт і дещо нижче рівня.
Екскаватор з обладнанням "зворотна лопата" (рис. 2) розробляє ґрунти нижче рівня стоянки. Розвантаження можна також здійснювати у відвал або транспорт, однак останній процес відбувається дещо складніше.
Робоче обладнання має шарнірне закріплену на поворотній платформі стрілу 7. Стріла шарнірно з'єднана з рукояткою 5 і з ковшем 6. Лебідка має барабани 1 і 3, на які намотуються підіймальний 2 та тяговий 4 канати. Коли один із барабанів загальмовано, а на другому відбувається намотування або змотування каната, стріла і рукоятка повертаються одночасно. Копання відбувається за рахунок повороту рукоятки. У кінці копання ковш з ґрунтом підтягується до стріли, піднімається вгору шляхом повертання рукоятки й здійснюється розвантаження ковша. Потім робоче обладнання повертається і цикл відновлюється.
Екскаватор-драглайн розробляє ґрунти нижче рівня стоянки й навіть під водою. Його використовують для влаштування глибоких виїмок, але глибина копання обмежена канатомісткістю барабана. Драглайн обладнують стрілою 3, шарнірно закріпленою на поворотній платформі. Стріла утримується і повертається за допомогою барабана 1 і каната 2. Ковш 5 драглайна оснащений аркою і підвішений на підіймальному 4 та тяговому 7 канатах, які намотуються на барабани 10 і 8. Канати закріплюються на ковші лан- цюгами. Тяговий канат проходить через систему напрямних блоків 9. На пі- діймальному канаті закріплено блок, який охоплюється розвантажувальним канатом 6, один кінець якого закріплено на арці ковша 5, а другий – на тяговому канаті.
– Одноківшовий екс- каватор з обладнанням "зво- ротна лопата":
1 – підіймальний барабан і лебідки; 2 – підіймальний канат; 3 – тяговий барабан лебідки; 5 – тяговий канат; 5 – рукоятка; 6 – ківш; 7 – стріла
Рис. 3 – Одноківшовий екскава- тор з обладнанням драглайн: в – конструктивна схема; б – схема підвіски ковша; 1 – стріловий барабан і лебідки; 2 – канат підйому
стріли; 3 – стріла; 4, 6 – підіймальний і розвантажувальний канати; 5 – ківш; 7 – тяговий канат; 8 – тягова лебідка; 9 – система напрямних блоків; 10 – підіймальний барабан
Під час роботи, намотуючи на барабан підіймальний канат, піднімають ковш угору, а барабан тягового каната гальмується. У верхньому положенні при розгальмуванні барабана тягового каната ківш подібно до маятника від- хиляється від стріли. Коли підіймальний і тяговий барабани розгальмовані збільшити радіус копання. При опусканні ковша ударяється аркою і перекидається на днище. При намотуванні тягового каната на барабан ківш драг- лайна пересувається по ґрунту, у результаті відбувається копання, подібне до ковша скрепера. Цю операцію виконують згори вниз, проте можна й у горизонтальній площині.
Коли ковш наповнюється ґрунтом, його піднімають, намотуючи підіймальний канат на барабан і пригальмовуючи тяговий барабан.
При цьому натягуються тяговий і розвантажувальний канати, що захищає ковш від перекидання та його розвантаження. Розвантаження ковша відбувається шляхом його повороту при розгальмуванні тягового барабана.
Грейферне екскаваторне обладнання використовують для копання коло- дязів з вертикальними стінками і для розробки глибоких виїмок. Для цього механічному екскаваторі встановлюють канатний грейфер, заглиблення ковша в ґрунт відбувається під дією його маси. Тому таке обладнання часто використовують при завантаженні.
Засоби сигналізації:У відповідності про призначення, обсягом, складом робіт і періодичністю їхнього виконання профілактичні роботи розділяються на планово-попереджувальні роботи (ППР) і позапланові. До складу планово-попереджувальних робіт входять: щозмінне (щодобове) технічне обслуговування приладів, виконуване протягом всієї зміни (доби); періодичне технічне обслуговування, виконуване відповідно до плану-графіка.
Щозмінне (щодобове) технічне обслуговування являє собою комплекс заходів, спрямованих на створення найбільш сприятливих умов для роботи засобів і систем контролю і автоматичного керування; поточне обслуговування полягає в систематичному виконанні операцій, які забезпечують нормальне функціонування засобів автоматизації (заливання чорнила, заправлення папером і т.п.), і у виявленні дефектів, що виникають при експлуатації приладів і засобів автоматизації.
Періодичне технічне обслуговування приладів і засобів автоматизації (періодичні перевірки) проводяться відповідно до затвердженого графіка планово-попереджувальних робіт, розроблювальному у залежності від характеру виробництва й режиму роботи (змінності) на підприємствах. В обсяг робіт при проведенні періодичної перевірки входять: огляд приладу для визначення його технічного стану, перевірка точності приладу й визначення при необхідності відповідного виду ремонту.
Позапланові роботи зводяться в основному до оперативного ремонту або заміни засобів, що відмовили, КВП і А. Перевірка точності показань приладів виробляються відповідно до норм, передбаченими ДЕРЖСТАНДАРТом, інструкціями Комітету стандартів, мір і вимірювальних приладів або технічних умов, зазначеними у монтажно-експлуатаційних інструкціях. Частіше по технічному стані прилад не вимагає поточного або капітального ремонту, період його експлуатації продовжується до наступної планової перевірки.
У відповідності про призначення, характером та обсягом виконуваних робіт ремонти розділяються на наступні види: поточний і капітальний.
При поточному ремонті виробляється усунення дрібних дефектів і окремих несправностей у вузлах, що перешкоджають нормальній роботі приладу. Поточний ремонт передбачає чищення приладу і часткове його розбирання та заміну ушкоджених дрібних деталей і вузлів. У випадку ремонту вимірювальної частини приладу виробляється обов'язкова його перевірка. Поточний ремонт виробляється вилами ремонтно-перевірочної ділянки служби КВП і А або безпосередньо на місці, без зняття приладу з установки, або у ремонтній майстерні. В останньому випадку заповнюється дефектний ярлик за підписом відповідальної особи ремонтної служби.
При капітальному ремонті приладу доводиться заміняти основні деталі, робити регулювання і припасування як механічних деталей так і електричних схем. Капітальний ремонт доцільно проводити для приладів з періодичністю перевірок не менш одного року.
Якість капітального ремонту й порядок приймання приладів повинні відповідати ДЕРЖСТАНДАРТу, інструкціям Комітету стандартів, вимірювальні прилади або технічні умови, установленим для нових приладів. Після капітального ремонту контрольно-вимірювальні прилади підлягають перевірці та здачі Гостповірювачу.
Ремонт приладів може вироблятися двома способами: індивідуальним та знеособленим.
При індивідуальному способі основні деталі і вузли після їхнього ремонту встановлюються на той же прилад, з якого вони були зняті.
При знеособленому способі ремонту заміна окремих деталей і вузлів у приладі виробляється за рахунок відремонтованих деталей і вузлів, раніше знятих з інших приладів, або з нових деталей і вузлів.
Індивідуальний спосіб ремонту застосовується для приладів, що надходять у ремонт невеликими партіями.
Знеособлений спосіб ремонту, будучи більш прогресивним, дозволяє організувати технологічний процес ремонту приладів з максимальною механізацією робіт, знижує трудомісткість і вартість ремонтів. При застосуванні знеособленого способу ремонту створюються необхідні фонди оборотних деталей і вузлів.
Як при індивідуальному, так і при знеособленому способах ремонту застосовується вузловий метод ремонту приладів. При цьому методі ремонту окремі деталі й вузли у міру виникнення потреби в їхньому капітальному ремонті знімаються і заміняються запасними, заздалегідь відремонтованими або новими.
Вузловий метод ремонту приладів застосовується для приладів, які конструктивно розчленовуються на вузли.
На підприємствах промисловості застосування того або іншого способу ремонту залежить від парку вимірювальних і регулюючих приладів на даному підприємстві.
Організація робіт з технічного обслуговування й ремонту передбачає: централізований ремонт приладів (підрядний спосіб), що виробляється на спеціалізованих заводах з ремонту приладів для підприємств даного економічного району або в спеціалізованих цехах з ремонту контрольно–вимірювальних приладів у регулюючих пристроїв, що обслуговують підприємства даного району. Ремонт приладів, здійснюваний підрядним способом, виробляється на підставі договорів або замовлень; ремонт у цехах КВП і А (господарський спосіб) по обслуговуванню й ремонту приладів даного підприємства (ремонт виробляється силами ремонтно-перевірочної ділянки служби КВП і А.
Доцільність застосування того або іншого виду ремонту залежить від наявного парку вимірювальних і регулюючих приладів даного підприємства, наявності в економічному районі підприємств централізованого ремонту та інших факторів.
Централізований ремонт приладів на спеціалізованих підприємствах і в цехах КВП і А є основною формою організації профілактичних і ремонтних робіт.
Правильна організація робіт з технічного обслуговування й ремонту приладів на підприємствах передбачає виконання наступних заходів: ведення систематичного обліку періодичних і державних перевірок і ремонтів за графіком до журналів періодичних перевірок і ремонтів своєчасне відбиття в технічних паспортах даних по перевірках і ремонту приладів; створення необхідного запасу деталей, матеріалів і вузлів; ведення обліку витрат запасних частин і матеріалів; оснащення необхідним устаткуванням, пристосуваннями та інструментом; забезпечення необхідними робочими кресленнями, інструкціями, технічними умовами, технологічною й іншою документацією, та нормативами на ремонт.
Періодичні перевірки, поточні ремонти, проведені без зняття приладу з установки, виконуються на об'єктах персоналом, спеціально виділений із числа експлуатаційно-обслуговуючої ділянки.
Поточні ремонти приладів, які не можна провести без зняття приладу з установки, виконуються силами ремонтно-перевірочної ділянки служби КВП і А підприємства. Проведення періодичних перевірок і ремонтів повинне вироблятися відповідно до затвердженого плану-графікові в дотикальному порядку, якщо на цей термін прилад відробив установлене число годин. При цьому періодичні перевірки виконуються у встановленому обсязі робіт, а ремонти виконуються в обсязі, виявленому при огляді. На кожний поступивший в експлуатацію прилад складається акт про надходження його на підприємство; одночасно приладу привласнюється інвентарний номер, що зберігається на весь період його експлуатації.
На кожний прилад заповнюється паспорт за формою, розробленої Комітетом стандартів, мір і вимірювальних приладів. Паспорт ведеться протягом усього терміну служби приладу і є постійно діючим документом службовцем для обліку й спостереження за станом приладу в експлуатації, а також для запису результатів його періодичних і державних перевірок та ремонту.
До обслуговування приладів допускаються особи, що знають конструкцію приладу й правила експлуатації та мають відповідну кваліфікаційну підготовку.
Для кращого збереження приладів, правильної експлуатації й підтримки їх у гарному технічному стані прилади закріплюються за обслуговуючим персоналом.
З метою відновлення нормальної роботи окремих приладів або систем при виході їх з ладу необхідно мати на підприємстві певну кількість запасних деталей і приладів. Визначення кількості запасних деталей і приладів, необхідних для проведення відбудовних робіт протягом даного періоду експлуатації з необхідною гарантійною ймовірністю того, що отриманої кількості досить на зазначений період експлуатації, виробляється в наступній послідовності: по розглянутій групі приладів, установлених на підприємстві, визначається кількість однотипних елементів - деталей або приладів (N); по таблицях відшукується значення інтенсивності відмов елементів даної групи (λ); обчислюється значення кількості запасних деталей або приладів по формулі:
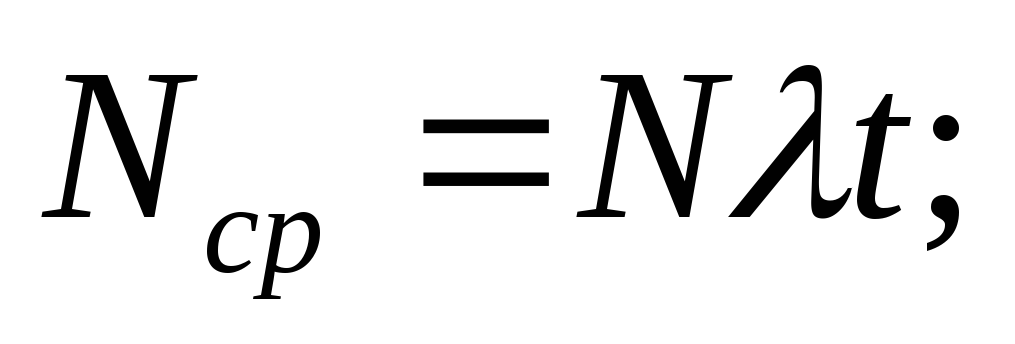
де t - період часу експлуатації, прийнятий рівним одного року (або сезону), у годинах; за графіком (мал. 26), визначається гарантоване число запасних деталей використовуючих приладів (Nгар) являється функцією Nср та гарантійної ймовірності (ά).
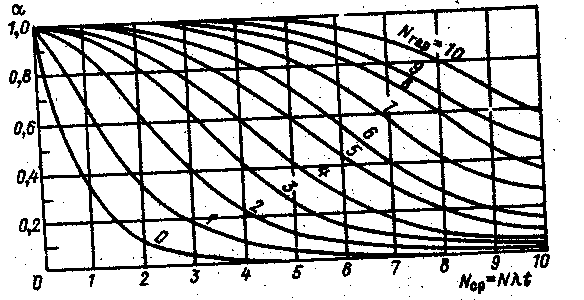
Рис. 26. Графік визначення числа запасних деталей і приладів.
Значення ά приймають рівним 0,9 - 0,95. Отримане число Nгар і є кількістю запасних деталей або приладів даного типу, які варто мати на підприємстві.
Для обслуговування й ремонту приладів і засобів автоматики в службі КВП і А можуть використовуватися слюсарі з ремонту приладів і засобів автоматизації, електромонтери-ремонтники, слюсарі-інсрументальники, електромонтери телефонного зв'язку і сигналізації й електромонтери по радіоустановках.
Загальне число працівників служби КВП і А залежить від сумарної трудомісткості, розрядів і періодичності робіт з урахуванням можливого розвитку систем автоматизації на підприємстві та розширення парку приладів.
Чисельність персоналу служби КВП і А підприємства, включаючи інженерно-технічних працівників, орієнтовно може бути визначена в наступних границях:
Цех КВП і А, категорія А – понад 35 чол.,
Цех КВП і А, категорія Б – 22 – 35 чол.,
Лабораторія КВП і А, категорія В – 16 - 21 чол.,
Лабораторія КВП і А, категорія Г – 8 - 15 чол.,
Група КВП і А, категорія Д – до 8 чол.
При організації служби КВП і А варто застосовувати уточнений метод розрахунку чисельності персоналу на різних ділянках служби.
Явочна чисельність чергового персоналу ділянки експлуатації в зміну визначається по формулі:

де А – сумарні витрачені часи на поточне обслуговування засобів автоматизації, вироблене одного разу у зміну або частіше, чол*хв/змін.; Б1,Б2,Б3,…Бі' – сумарні витрати часу на поточне обслуговування засобів автоматизації, вироблене рідше одного разу в зміну, чол-хв.; п,пг,.,.,п. – кількість робочих змін в інтервалі часу між двома черговими обслуговуваннями одних і тих же приладів; З-С-тривалість однієї зміни, хв/змін ; ДО3 - коефіцієнт запасу, що враховує необхідність виконання непередбачених робіт, (ДО3= 1,1 - якщо засоби автоматизації встановлені в приміщеннях; ДО3 = 1,15 - якщо засоби автоматизації встановлені у приміщеннях з відносною вологістю більше 60%або є хімічно активні середовища або пил.)
Облікова чисельність чергового персоналу в добу, про облік підмінного персоналу, визначається так:
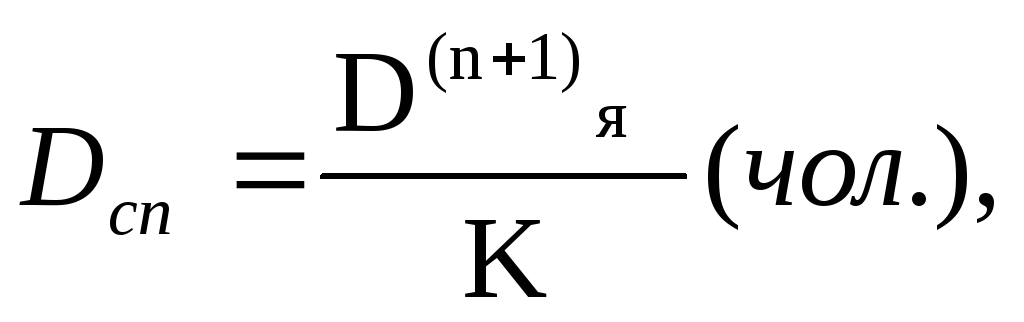
де n - число робочих змін у добу; ДО – коефіцієнт облікового штату робітників, ДО=Э/Н; Э - ефективний фонд робочого часу одного працівника в рік (година); Н - номінальний фонд часу.
Для робітників, що мають 12-денну додаткову відпустку при 7-вартовому робочому дні, варто приймати Э1 = 1795 годину. ДО1, = 0,85; при 6-денній додатковій відпустці: Э2= 1851 година., Кг=0,87; при відсутності додаткової відпустки: Э3 = 1893 год., ДО3 = 0,89; при 12-денній додатковій відпустці й 6-годинному робочому дні: Э4= 1590 година., ДО4=0,87.
Явочна чисельність персоналу, що виконує перевірочні, пусконалагоджувальні, ремонтні роботи й техогляди, визначається:
Ря =Бр·К3/Э (чол. в год);
де Бр- сумарні витрати часу на ремонтні, перевірочні, пусконалагоджувальні роботи й техогляди, виконувані персоналом певної кваліфікації протягом року, чол-годин.
Облікова чисельність персоналу, що виконує перевірочні, пусконалагоджувальні, ремонтні роботи й техогляди, визначається:
Рсп=Ря/ДО (чол. у рік)
Для сезонних виробництв, на яких черговий персонал залучається до ремонтних робіт у період простою заводу, облікова чисельність ремонтного персоналу визначається:
Рсп.с=Рсп.-Кн( 1-тр)Dсп.
де Тр - період роботи заводу в частках року; Кн - коефіцієнт, що враховує деякої втрати, випробовувані ремонтною службою КВП і А в зв'язку про недостатню підготовленість чергового персоналу до ремонтних робіт і нерівномірністю самих робіт. Значення Кн приймається рівним 0,85.